روانکاری بلبرینگ
روانکاری بلبرینگ یکی از جنبههای مهم برای بهبود عملکرد و طول عمر آنها است. روانکارها باعث کاهش اصطکاک بین اجزای متحرک بلبرینگ میشوند، که این امر به کاهش سایش و گرما کمک میکند و در نتیجه کارکرد بلبرینگها بهبود مییابد. انواع مختلفی از روانکارها وجود دارند که میتوانند بسته به نوع کاربرد و شرایط محیطی استفاده شوند:
روانکارهای مایع (روغنها): برای بلبرینگهایی که در سرعتهای بالا و یا دماهای بالا کار میکنند، روغنهای مخصوص معمولاً استفاده میشوند. این روغنها به صورت دائمی یا به صورت دورهای تجدید میشوند.
روانکارهای جامد (چربیها): چربیها معمولاً در بلبرینگهایی که نیاز به نگهداری کمتر دارند یا در شرایطی که روغن نمیتواند به راحتی توزیع شود، استفاده میشوند. این روانکارها به حفظ چربی در بلبرینگ کمک کرده و باعث کاهش سایش میشوند.
روانکارهای ترکیبی: در برخی موارد، ترکیبی از روغن و چربی برای داشتن مزایای هر دو نوع روانکار استفاده میشود.
انتخاب نوع روانکار بستگی به عواملی همچون سرعت، دما، فشار و شرایط محیطی (مانند رطوبت یا گرد و غبار) دارد. همچنین، باید دقت کرد که روانکار به درستی و به مقدار مناسب استفاده شود تا از عملکرد مطلوب بلبرینگها اطمینان حاصل شود.
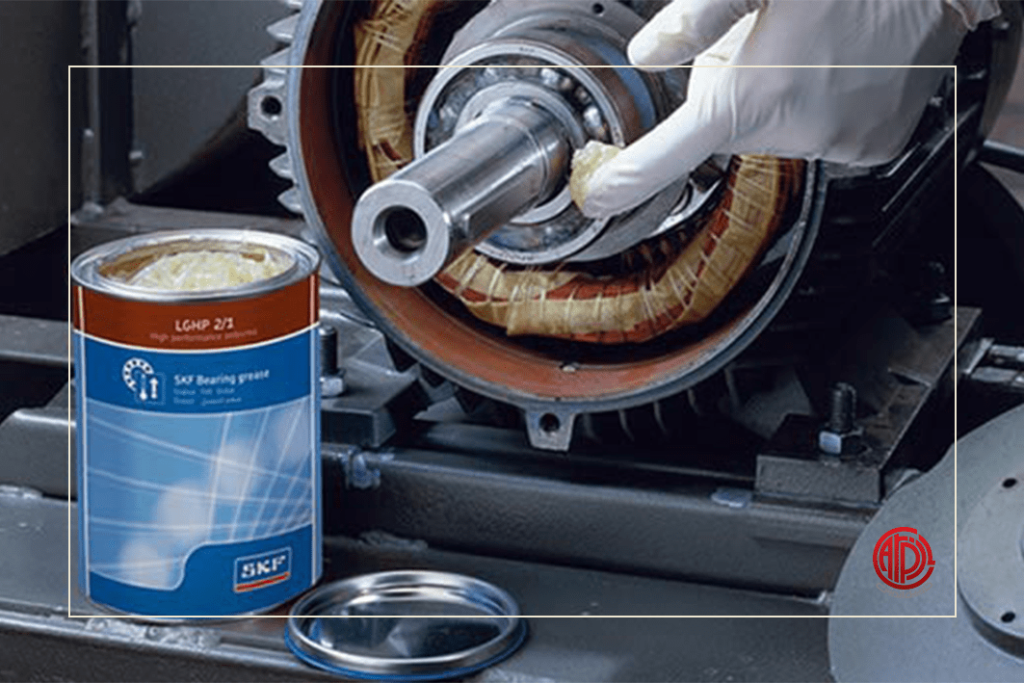
روش روانکاری بلبرینگ
روشهای روانکاری بلبرینگ به چندین عامل مانند نوع بلبرینگ، شرایط کارکرد (سرعت، بار، دما) و محیط کاری بستگی دارد. انتخاب روش مناسب برای روانکاری میتواند عمر مفید بلبرینگها را افزایش دهد و عملکرد آنها را بهبود بخشد. در اینجا به برخی از روشهای رایج روانکاری بلبرینگها اشاره میکنم:
روغنکاری با پمپ (روغن مایع)
در این روش، روغن به طور مداوم توسط یک پمپ یا سیستم گردش روغن به بلبرینگها وارد میشود. این روش معمولاً برای بلبرینگهایی که در سرعتهای بالا یا دماهای زیاد کار میکنند، مانند بلبرینگهای موتورهای الکتریکی و توربینها استفاده میشود.
- مزایا: کاهش اصطکاک و گرما، عملکرد پایدار، مناسب برای شرایط دمایی بالا.
- معایب: هزینه بالاتر نصب و نگهداری سیستم پمپی.
چربیکاری (روانکاری با چربی)
این روش در بلبرینگهایی که نیاز به روانکاری کمتر و عملکرد مستمر دارند، رایج است. در این روش، چربی به داخل بلبرینگها اعمال میشود. چربیها معمولاً به صورت خودکار یا دستی به بلبرینگها اضافه میشوند و در برخی از موارد ممکن است نیاز به تعویض دورهای داشته باشند.
- مزایا : نگهداری آسانتر، مناسب برای بلبرینگهایی که در سرعتهای پایینتر یا بارهای سنگینتر کار میکنند.
- معایب : احتمال گرم شدن چربی در شرایط دمایی بسیار بالا، نیاز به توجه به میزان چربی موجود.
روانکاری خودکار (Self-lubricating Bearings)
در این نوع، بلبرینگها دارای ساختاری هستند که به طور خودکار روغن یا چربی را به بیرون یا داخل بلبرینگ منتقل میکنند. این نوع بلبرینگها بیشتر در محیطهایی با دسترسی سخت به روانکارها استفاده میشوند.
- مزایا: کاهش نیاز به نگهداری دستی، عملکرد مداوم بدون نیاز به سرویسهای مکرر.
- معایب: هزینه بالاتر، نیاز به محیطهای خاص برای نصب.
روانکاری با قطرهای (Drop lubrication)
در این روش، روغن به صورت قطرهای به بلبرینگها اضافه میشود. این روش معمولاً برای بلبرینگهایی با سرعت متوسط و بار کم تا متوسط کاربرد دارد.
- مزایا: ساده و ارزان، برای کاربردهایی با سرعت متوسط و بار کم مناسب است.
- معایب: نیاز به دقت در مقدار و زمان بندی برای جلوگیری از کمبود یا زیاد بودن روغن.
روانکاری با هوا (Air lubrication)
این روش به ویژه در بلبرینگهایی که تحت شرایط بسیار خاص (مانند سرعتهای بسیار بالا یا در محیطهای خاص مثل خلاء) کار میکنند، مورد استفاده قرار میگیرد. در این روش، هوا یا گاز به عنوان روانکار عمل میکند.
- مزایا: کاهش شدید اصطکاک، مناسب برای سرعتهای بسیار بالا.
- معایب: نیاز به تجهیزات خاص و پیچیده، هزینه بالا.
روانکاری با غوطهوری (Immersion Lubrication)
در این روش، بلبرینگها به طور کامل در مایع روانکار غوطهور میشوند. این روش برای بلبرینگهایی که در شرایط دمایی بالای دائم کار میکنند یا در کاربردهایی با بارهای زیاد مورد استفاده قرار میگیرد.
- مزایا: روغن به طور یکنواخت توزیع میشود، کنترل دقیق شرایط روانکاری.
- معایب: نیاز به سیستمهای نگهداری و تعمیرات پیشرفته.
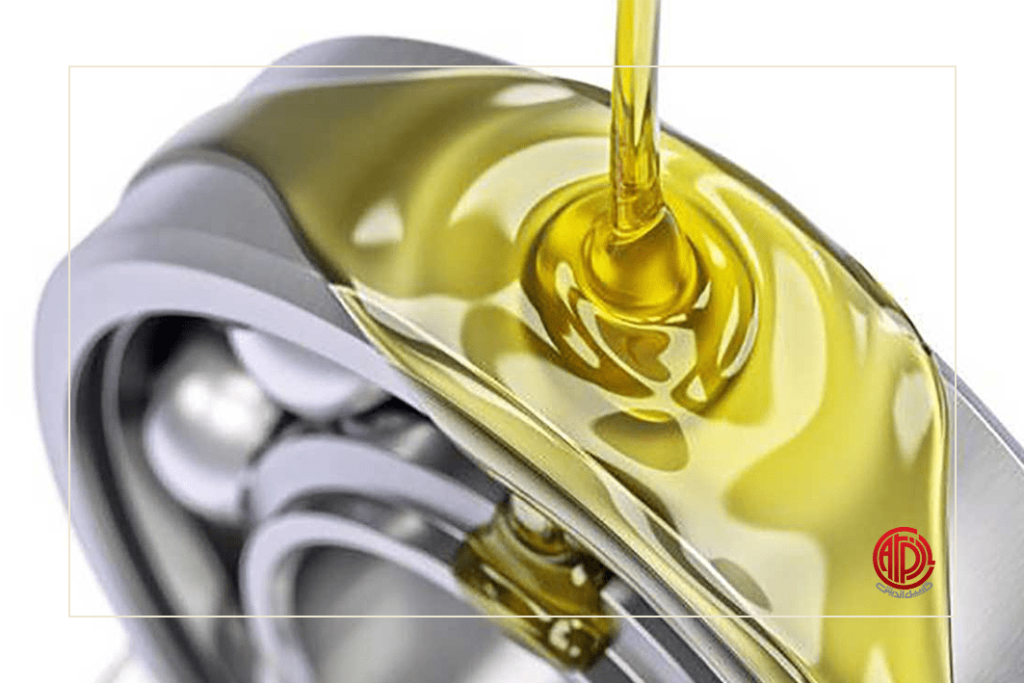
روانکاری بلبرینگ چرخشی (Centrifugal Lubrication)
در این روش، روغن از طریق حرکت چرخشی بلبرینگ به داخل آن وارد میشود. این روش بیشتر در کاربردهایی استفاده میشود که در آن بلبرینگها در سرعتهای بالا حرکت میکنند.
- مزایا: توزیع یکنواخت روانکار، مناسب برای سرعتهای بالا.
- معایب: نیاز به طراحی خاص و تنظیم دقیق سیستم.
نکات مهم در انتخاب روش روانکاری:
- سرعت: برای بلبرینگهای با سرعت بالا، معمولا روغن مایع یا سیستمهای خاص مانند هوا یا روغن پمپی برای روانکاری بلبرینگ مناسبتر هستند.
- دما: در محیطهای با دمای بالا، روغنها یا چربیهایی که توانایی مقاومت در دماهای بالا را دارند، باید انتخاب شوند.
- بار: در صورتی که بلبرینگ تحت بارهای سنگین قرار گیرد، چربیها یا روغنهای خاصی که تحمل بار بالاتر را دارند، باید مورد استفاده قرار گیرند.
- نوع محیط: در محیطهای آلوده، روغنها و چربیهایی که مقاومت به گرد و غبار یا رطوبت دارند، باید استفاده شوند.
انتخاب روش مناسب برای روانکاری بستگی به نیاز خاص ماشینآلات و شرایط کارکرد دارد.
مناسبترین گریس برای روانکاری بلبرینگ
مناسبترین گریس برای بلبرینگها بستگی به عوامل مختلفی مانند نوع بلبرینگ، شرایط کارکرد، سرعت، دما و بار دارد. هر نوع گریس ویژگیهای خاصی دارد که میتواند عملکرد بلبرینگها را تحت تأثیر قرار دهد. به طور کلی، گریسها از ترکیب روغن پایه، مواد افزودنی (مانند ضد سایش، ضد خوردگی) و ماده غلیظکننده (مانند لیتیم، کلسیم یا آلومینیوم) تشکیل میشوند. در اینجا به برخی از انواع گریسهای رایج و کاربردهای آنها اشاره میکنم:
گریسهای لیتیوم (Lithium Grease)
گریسهای لیتیوم یکی از رایجترین انواع گریسها هستند و به طور گسترده در بلبرینگها و دیگر تجهیزات صنعتی استفاده میشوند. این گریسها به دلیل پایداری بالا، مقاومت به دما و آب، و ویژگیهای عالی در کاهش اصطکاک محبوب هستند.
- ویژگیها: مقاومت عالی در برابر دماهای بالا (تا حدود 120°C)، مقاومت در برابر رطوبت، عمر طولانی.
- کاربرد: بلبرینگهای صنعتی، خودروها، موتورهای الکتریکی و پمپها.
گریسهای کلسیم (Calcium Grease)
گریسهای کلسیم معمولاً برای شرایطی که نیاز به مقاومت در برابر آب و رطوبت دارند، استفاده میشوند. این گریسها معمولاً در محیطهای مرطوب یا با تماس مستقیم با آب کاربرد دارند.
- ویژگیها : مقاومت خوب در برابر آب، مناسب برای شرایط مرطوب، پایداری در برابر سایش.
- کاربرد : بلبرینگهای ماشینآلات کشاورزی، سیستمهای رطوبتی، صنایع دریایی.
- ZWZ Bearing
- استاندارد بلبرینگ چینی
- استعلام قیمت بلبرینگ
- انواع برند بلبرینگ
- انواع بلبرینگ zwz
- انواع بلبرینگ چینی
- انواع بلبرینگ و رولبرینگ
- انواع بلبرینگ*
- انواع سایزهای بلبرینگ
- انواع مختلف بلبرینگ
- بادوامترین بلبرینگ
- برترین برندهای بلبرینگ
- برترین بلبرینگ
- برترین سایت بلبرینگ
- برترین سایت بلبرینگ چینی
- برند zwz
- برند های بلبرینگ چینی
- بلبرینگ
- بلبرینگ skf
- بلبرینگ zwz
- بلبرینگ ارزان
- بلبرینگ ارزان قیمت
- بلبرینگ استوانه ای چیست ؟
- بلبرینگ اصل
- بلبرینگ اقتصادی
- بلبرینگ با کیفیت چینی
- بلبرینگ باکیفیت
- بلبرینگ به صرفه
- بلبرینگ تماس زاویه ای دوطرفه
- بلبرینگ چیست ؟
- بلبرینگ چینی
- بلبرینگ چینی اصل
- بلبرینگ چینی باکیفیت
- بلبرینگ چینی درجه یک
- بلبرینگ خود تنظیم شونده
- بلبرینگ درجه 1 چینی
- بلبرینگ زد دبلیو زد
- بلبرینگ ساخت چین
- بلبرینگ ساخت چین
- بلبرینگ شیار عمیق
- بلبرینگ شیار عمیق چیست ؟*
- بلبرینگ صنعتی
- بلبرینگ صنعتی zwz
- بلبرینگ کف گرد
- بلبرینگ کف گرد چیست ؟
- بلبرینگ مناسب قیمت
- بلبرینگ نسوز*
- به صرفه ترین خرید بلبرینگ
- بهترین برند برای خرید بلبرینگ چینی کدام است ؟
- بهترین برند بلبرینگ چینی
- بهترین بلبرینگ چینی
- بهترین راه برای اطمینان از بلبرینگ ؟
- بهترین قیمت بلبرینگ چینی
- بهترین گریس برای بلبرینگ
- پخش بلبرینگ چینی
- پخش کننده بلبرینگ در تهران
- پرداخت
- پمپ صنعتی
- تاریخچه بلبرینگ
- تامین کننده بلبرینگ
- تجهیزات صنعتی
- تست بلبرینگ
- تست بلبرینگ چینی
- تضمین اصالت بلبرینگ
- تماس با ما :
- توربین بادی
- جنس بلبرینگ
- حساب کاربری
- حفاری معادن ، سیمان ، فولاد
- حمل و نقل ریلی
- خرید بلبرینگ
- خرید بلبرینگ zwz
- خرید بلبرینگ به صرفه
- خرید بلبرینگ چینی
- خرید بلبرینگ در تهران
- خرید عمده بلبرینگ چینی
- درباره ما
- راحت ترین راه برای نصب بلبرینگ
- روش نصب بلبرینگ
- روغن کاری بلبرینگ
- رولبرینگ zwz
- رولبرینگ استوانه ای**
- رولبرینگ بشکه ای
- رولبرینگ بشکه ای*
- رولبرینگ تماس زاویه ای**
- رولبرینگ مخروطی
- ساخت بلبرینگ
- سایت بلبرینگ
- سایز بلبرینگ
- سایز های بلبرینگ چینی
- سبد خرید
- شرکت کارپیل اندیش نماینده رسمی دو برند ZWZ , TMB
- صنعت نفت و گاز و پتروشیمی
- عرضه کننده بلبرینگ
- عوامل مهم در انتخاب بلبرینگ
- عوامل موئثر بر قیمت بلبرینگ چیست ؟
- فروش اینترنتی بلبرینگ
- فروش بلبرینگ
- فروش بلبرینگ به صرفه
- فروش بلبرینگ چینی
- فروش بلبرینگ صنعتی
- فروشگاه بلبرینگ
- قیمت zwz
- قیمت بلبرینگ zwz
- قیمت بلبرینگ استوانه ای
- قیمت بلبرینگ استوانه ای zwz
- قیمت بلبرینگ تماس زاویه ای
- قیمت بلبرینگ چین چطور محاسبه میشه ؟
- قیمت بلبرینگ چینی
- قیمت بلبرینگ چینی zwz
- قیمت بلبرینگ خود تنظیم شونده
- قیمت بلبرینگ شیارعمیق
- قیمت بلبرینگ صنعتی
- قیمت بلبرینگ کف گرد
- قیمت رولبرینگ بشکه ای
- قیمت رولبرینگ مخروطی
- کار با بلبرینگ
- کاربرد بلبرینگ در صنعت
- کاسه نمد
- کیفیت بلبرینگ چینی
- لیست قیمت بلبرینگ چینی
- لیست محصولات بلبرینگ های کف گرد
- ماشین آلات سبک،سنگین
- مشخصات نمایندگی رسمی بلبرینگ
- معروفترین بلبرینگ چینی
- مقایسه بلبرینگ سرامیکی و فولادی
- مقرون به صرفه ترین بلبرینگ
- نکات مهم در خرید بلبرینگ ZWZ چیست ؟
- نمایندگی بلبرینگ
- نمایندگی بلبرینگ چینی
- نمایندگی رسمی zwz
- نمایندگی رسمی بلبرینگ
- نمایندگی معتبر بلبرینگ
- نماینده رسمی بلبرینگ TMB
- نماینده رسمی بلبرینگ های ZWZ
- نماینده فروش بلبرینگ
- همه چیز درباره خریداری بهترین بلبرینگ ؟
- وارد کننده بلبرینگ
- واردات بلبرینگ چینی
- واردکننده بلبرینگ صنعتی در ایران
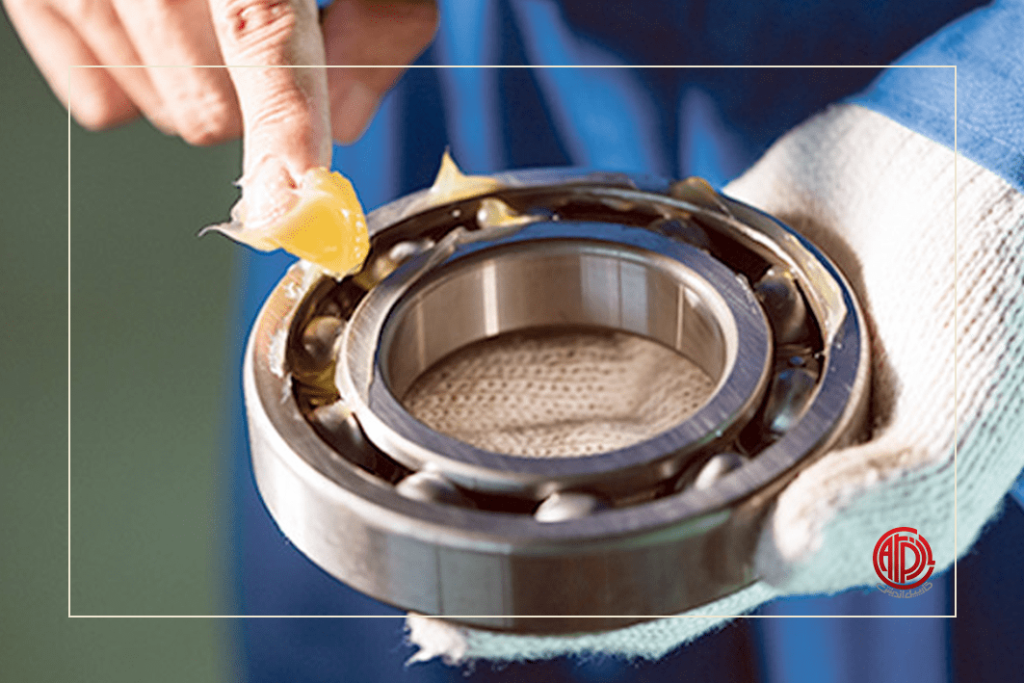
گریسهای آلومینیوم (Aluminum Complex Grease)
گریسهای آلومینیوم برای شرایط دمایی بالا و فشار زیاد مناسب روانکاری بلبرینگ هستند. این نوع گریسها مقاومت عالی در برابر حرارت دارند و در دماهای بالاتر از گریسهای لیتیومی عملکرد بهتری دارند.
- ویژگیها : مقاومت بالا در دماهای زیاد (تا حدود 180°C)، پایداری در برابر بارهای سنگین.
- کاربرد : بلبرینگهای صنعتی که در دماهای بالا کار میکنند، سیستمهای تحت فشار شدید.
گریسهای مصنوعی (Synthetic Grease)
گریسهای مصنوعی از ترکیب مواد پایه مصنوعی ساخته میشوند و در شرایطی که نیاز به پایداری بالاتر در دماهای بسیار بالا یا پایین، و یا در شرایط خاص محیطی (مانند خلا یا گازهای خورنده) وجود دارد، استفاده میشوند.
- ویژگیها : پایداری عالی در دماهای بسیار بالا یا پایین، مقاومت به مواد شیمیایی، عمر طولانی.
- کاربرد : بلبرینگهایی که در صنایع هوافضا، خودروهای پرسرعت، تجهیزات زیر دریایی و سیستمهای با شرایط سخت کار میکنند.
گریسهای با افزودنی ضد سایش (Anti-Wear Additive Grease)
این نوع گریسها دارای افزودنیهایی هستند که برای کاهش سایش و خوردگی طراحی شدهاند. این افزودنیها معمولاً شامل سولفید مولیبدن یا دیگر ترکیبات مشابه هستند که باعث میشود بلبرینگها در برابر فشارهای زیاد و سرعتهای بالا مقاومت بیشتری داشته باشند.
- ویژگیها : خاصیت ضد سایش، مناسب برای سرعتهای بالا و بارهای سنگین.
- کاربرد : بلبرینگهای تحت فشار شدید، موتورهای الکتریکی و تجهیزات صنعتی که در معرض شرایط سخت قرار دارند.
گریسهای مقاوم به آب و رطوبت (Water-Resistant Grease)
برای روانکاری بلبرینگهایی که در معرض تماس با آب یا رطوبت قرار دارند، گریسهای مقاوم به آب طراحی میشوند. این گریسها معمولاً برای جلوگیری از زنگزدگی و خوردگی در محیطهای مرطوب استفاده میشوند.
- ویژگیها: مقاوم به آب، جلوگیری از زنگزدگی، حفظ خواص روانکاری در شرایط مرطوب.
- کاربرد: بلبرینگهای ماشینآلات دریایی، ماشینآلات کشاورزی و تجهیزات تحت تماس با آب.
گریسهای ضد زنگ و ضد خوردگی (Corrosion-Resistant Grease)
این نوع گریسها معمولاً در محیطهای شیمیایی یا صنعتی که خطر خوردگی وجود دارد، استفاده میشوند. این گریسها مواد افزودنی ضد خوردگی دارند که به محافظت از اجزای بلبرینگ در برابر رطوبت و مواد شیمیایی کمک میکند.
- ویژگیها: خاصیت ضد خوردگی و ضد زنگ، مقاوم در برابر شرایط شیمیایی و رطوبتی.
- کاربرد: بلبرینگهای صنعتی، ماشینآلات کشاورزی و تجهیزات در معرض مواد شیمیایی.
درست ترین روش روانکاری بلبرینگ
روانکاری مناسب بلبرینگ برای اطمینان از عملکرد صحیح، افزایش طول عمر و کاهش اصطکاک و سایش بسیار مهم است. روشهای مختلفی برای روانکاری بلبرینگ وجود دارد که انتخاب روش مناسب بستگی به نوع بلبرینگ، شرایط کاری و محیط دارد. در ادامه مراحل و نکات کلیدی برای روانکاری صحیح بلبرینگ آورده شده است:
1. انتخاب نوع روانکار مناسب
- گریس: برای بیشتر بلبرینگها مناسب است، بهخصوص در سرعتهای پایین تا متوسط. گریس به دلیل خاصیت چسبندگی خود، درون بلبرینگ باقی میماند و نیاز به روانکاری مکرر را کاهش میدهد.
- روغن: برای سرعتهای بالا و دماهای بسیار بالا توصیه میشود. روغن جریان دارد و میتواند حرارت را بهتر دفع کند.
2. روشهای روانکاری بلبرینگ
✔️ روانکاری با گریس
- مقدار گریس نباید بیش از حد باشد؛ زیرا این امر میتواند باعث افزایش دما و کاهش کارایی بلبرینگ شود.
- برای پر کردن بلبرینگ با گریس، حدود 30 تا 50 درصد فضای داخلی آن کافی است.
- در بلبرینگهایی با سرعت بالا، حجم گریس کمتر (حدود 30 درصد) و در بلبرینگهای با سرعت پایین، حجم بیشتری (حدود 50 درصد) توصیه میشود.
✔️ روانکاری با روغن
- در این روش روغن باید به طور مداوم تأمین شده یا در فواصل مشخص تعویض گردد.
- روشهای تأمین روغن شامل روغنکاری قطرهای، غوطهوری، پاششی یا چرخشی است.
3. مراحل روانکاری بلبرینگ با گریس
- تمیزکاری: ابتدا بلبرینگ را با مواد شوینده مناسب کاملاً تمیز کرده و مطمئن شوید که گرد و غبار، آلودگی یا بقایای قدیمی در آن باقی نمانده است.
- خشککردن: بلبرینگ را کاملاً خشک کنید.
- اعمال گریس: مقدار مناسبی گریس را درون محفظه بلبرینگ و روی اجزای غلتشی قرار دهید.
- مونتاژ: پس از روانکاری، بلبرینگ را با دقت در جای خود نصب کنید.
- بررسی: پس از نصب، دستگاه را بهآرامی راهاندازی کرده و نشتی یا صداهای غیرعادی را بررسی کنید.
4. نکات مهم در روانکاری
✅ از روانکارهای ناسازگار با یکدیگر استفاده نکنید.
✅ نوع گریس یا روغن باید متناسب با دمای کاری، سرعت چرخش و بار وارده انتخاب شود.
✅ دورههای بازبینی و روانکاری مجدد را بر اساس شرایط کاری و توصیههای تولیدکننده تعیین کنید.
✅ در محیطهای آلوده، از آببندی مناسب برای جلوگیری از ورود گردوغبار و رطوبت استفاده کنید.
آیا به توضیحات تکمیلی در مورد انتخاب گریس یا روغن نیاز دارید؟
انتخاب گریس مناسب :
برای انتخاب مناسبترین گریس برای بلبرینگها، باید به چندین عامل توجه داشت:
دما : بسته به دمای کارکرد بلبرینگها، باید گریسی با پایداری دمایی مناسب انتخاب شود.
سرعت : برای سرعتهای بالا، گریسهای با ویسکوزیته پایین مناسبترند.
بار : برای بارهای سنگین، گریسهایی با افزودنیهای ضد سایش و مقاومت به فشار بالا بهتر عمل میکنند.
محیط کاری : در محیطهای مرطوب، حاوی گرد و غبار یا مواد شیمیایی، باید از گریسهای مقاوم به آب، ضد خوردگی یا مخصوص محیطهای خاص استفاده شود.
نکته مهم :
گریسها باید به مقدار مناسب و بهطور منظم جایگزین شوند تا عملکرد بلبرینگها بهینه باقی بماند. مقدار زیاد یا کم از گریس میتواند به عملکرد بلبرینگ آسیب برساند.
آدرس فروشگاه :
آدرس: سعدی جنوبی، خیابان اکباتان، کوچه ناظم الاطبا شمالی، پاساژ مبصر، طبقه همکف، پلاک 15
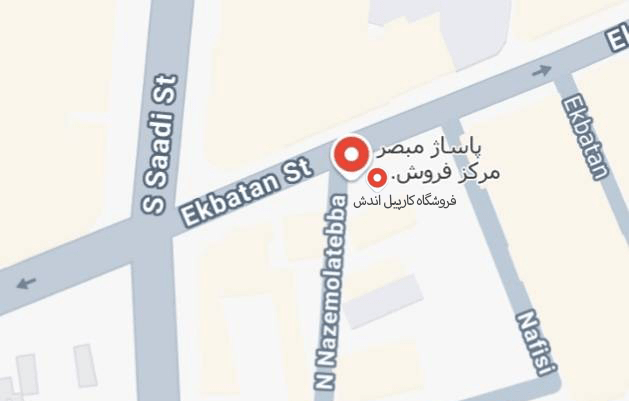
آدرس دفتر :
تهران ، شهرک غرب ، بلوار فرحزادی ، بلوار نورانی ، پلاک 36
تلفن فروشگاه :
021-33996881
021-33996882
تلفن دفتر :
021-88562390
021-88562210
ایمیل :
info @carpil-co.com
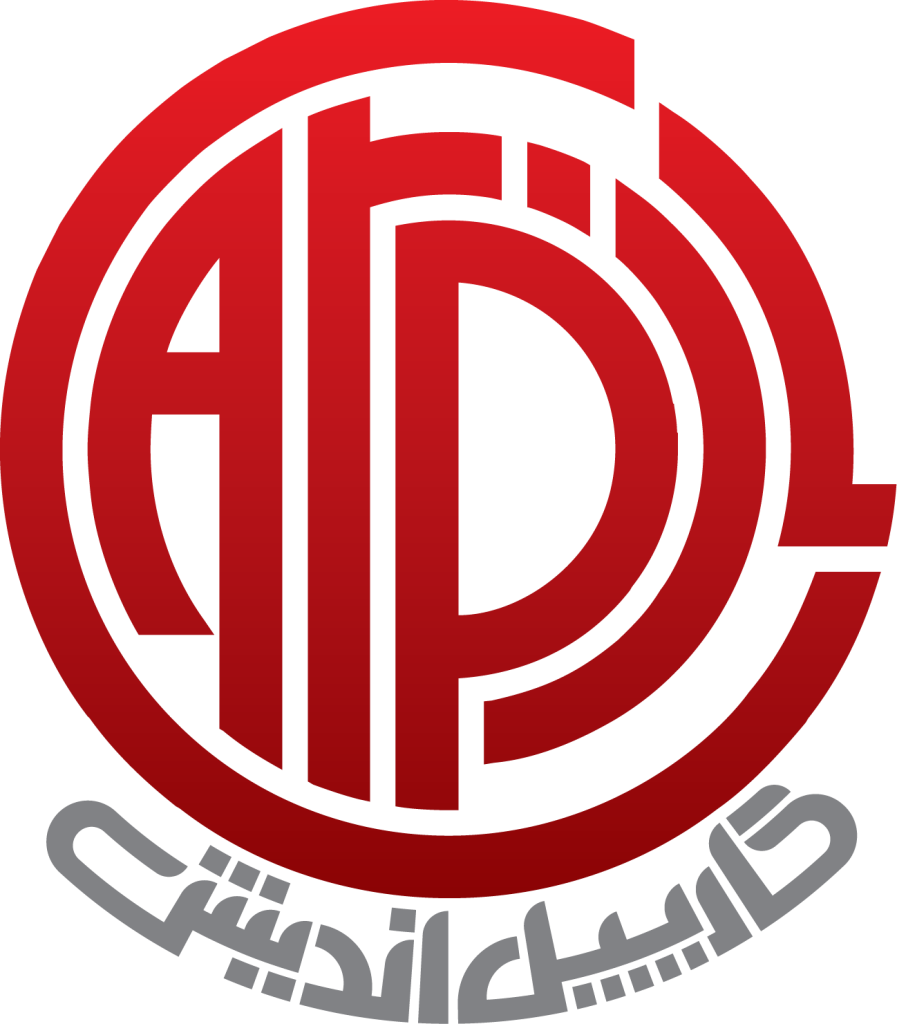
شبکه های اجتماعی ما :
واتساپ :
09199068526
تلگرام :
09199068526
اینستاگرام :
carpil andish
09
دیدگاهتان را بنویسید