طریقه ی روغن کاری بلبرینگ
شیوه روغن کاری بلبرینگ باید دقیق انتخاب و انجام شود. برای مطلع شدن از شیوه های مختلف و روش کار با ما در این مقاله همراه شوید . چرا که همه نکات ذکر شده به شما در به دست آوردن اطلاعات این زمینه کمک به سزایی دارد .
طریقه روغن کاری بلبرینگ به روش های مختلف
صنایع موجود در جهان از روش های گوناگون برای روغن کاری بلبرینگ های خود استفاده می کنند. طریقه روغن کاری بلبرینگ به روش های مختلفی طبقه بندی می شوند که به شرح هر یک می پردازیم. 5 روش زیر اصلی ترین موارد در این حوزه می باشند.
هیدرواستاتیکی
اگر سرعت حرکتی بین سطوح به نسبت قابل توجه باشد، این روش به کار گرفته می شود. نمونه کاربرد این طریقه روغن کاری بلبرینگ را می توان در بلبرینگ های لغزشی مشاهده کرد. طی این شرایط، کار روان کار سنگین نیست و صرفا باید در حجم مناسب و سرعت حرکت متعادل باشد.
طریقه روغن کاری بلبرینگ به روش هیدرودینامیک
در روش هیدرودینامیک به فشار بالای روان کار نیاز است. به کمک این فشار لایه ای از روان کار مابین سطوح حرکت کننده ایجاد می کردد و به این صورت میزان اصطکاک و سایش کاهش می یابد. این متد در هنگام شروع حرکت یا در سرعت های بالا به کار می رود.
الاستوهیدرودینامیک
در صورتی که حرکات نسبی سطح های روی هم غلتشی و هم چنین لغزشی باشد، این روش کاربردی است. از نمونه مواردی که روش الاستو هیدرودینامیک استفاده می گردد، می توان به غلتک، چرخنده، بادامک و بیرینگ های از نوع غلتشی، اشاره داشت.
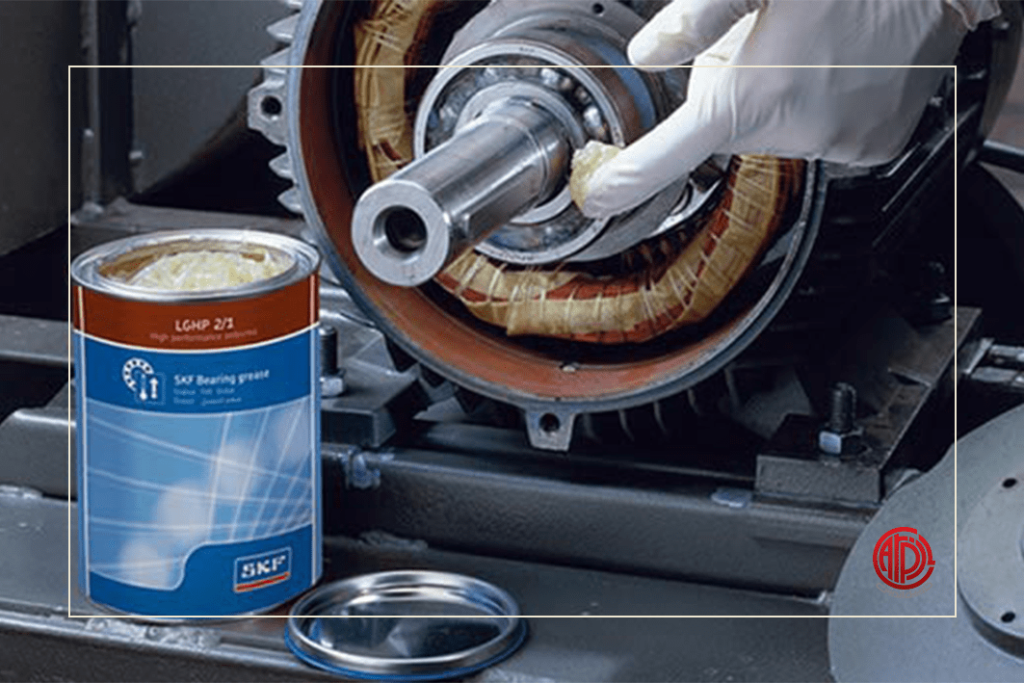
روانکاری مرزی
طریقه روغن کاری بلبرینگ به روش مرزی به طور معمول در صنایع به کار نمی رود؛ چرا که ضخامت لایه روغنی بسیار نازک است و تنها در حد چند مولکول می باشد. از این رو به آن روان کاری ناقص هم می گویند که خیلی روش کاربردی نمی باشد.
که روان کار جامد محسوب می گردد. در سال های اخیر این متد به واسطه مجموعه های معتبر در تولید بیرینگ عرضه می شود.
فرآیند روغن کاری یا روانکاری بلبرینگ چیست
معمولا چندین مرحله برای انجام روان کاری در سطوح بیرینگ طی می شود تا اطمینان حاصل شود روان کننده کاربرد و توزیع درستی دارد. در ادامه به صورت کلی این مراحل را بررسی می کنیم.
آماده سازی
پیش از شروع روغن کاری و انتخاب طریقه روغن کاری بلبرینگ، می بایست سطح مورد نظر را از هر گونه گرد و غبار و آلودگی پاک کنید. در غیر این صورت سطح مناسبی جهت روغن کاری اصولی نخواهید داشت. پس برای جلوگیری از بروز مشکل، حتما به این نکته خوب دقت کنید.
انتخاب روانکار
برای داشتن انتخابی درست در خصوص روان کار، باید به یکسری معیار و فاکتور توجه داشته باشید. از جمله این موارد به سرعت، میزان بار، دما و شرایط عملیاتی، می توان اشاره داشت.
کاربرد روان کننده
به کار گیری روان کار بسته به نوع آن و هم چنین طراحی بلبرینگ، روش های مختلف دارد. روش هایی که در ادامه توضیح می دهیم از برترین و عمومی ترین روش ها هستند.
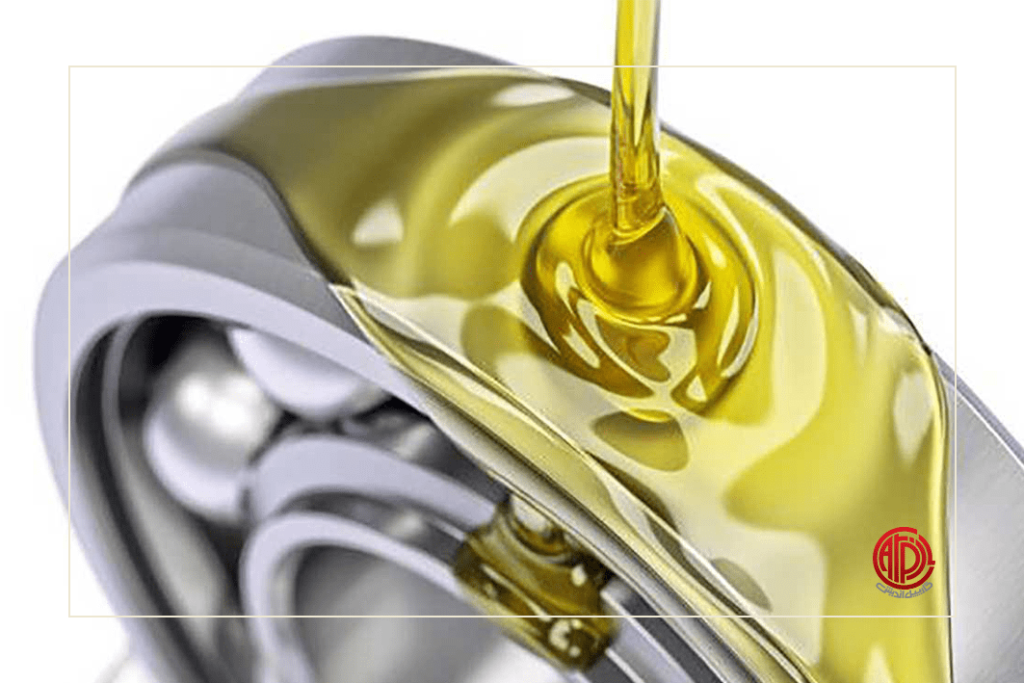
روانکاری دستی
در این روش از طریقه روغن کاری بلبرینگ، روغن کش ها، تفنگ روغن کاری یا دست استفاده می شود. به کمک این ابزارها می توان روان کننده را به طور مستقیم روی بیرینگ مالید. در صورت استفاده از گریس، مطمئن شوید که به خوبی فضای موجود پر گشته و توزیع به شکل مناسبی صورت گرفته است.
روانکاری خودکار
بسیاری از صنایع از روش اتوماتیک جهت روان کاری استفاده می شود. همانطور که از نام این روش برمی آید، به صورت خودکار روان کاری انجام می شود؛ به این صورت که این کار در 2 حالت فاصله زمانی منظم و یا تعیین پارامترهایی که به واسطه آن روغن کاری انجام شود، انجام می پذیرد. این روش در سه سیستم مختلف دیده می شود:سیستم روان کاری متمرکز، سیستم روغن کاری اسپری روغن و سیستم گریس خودکار.
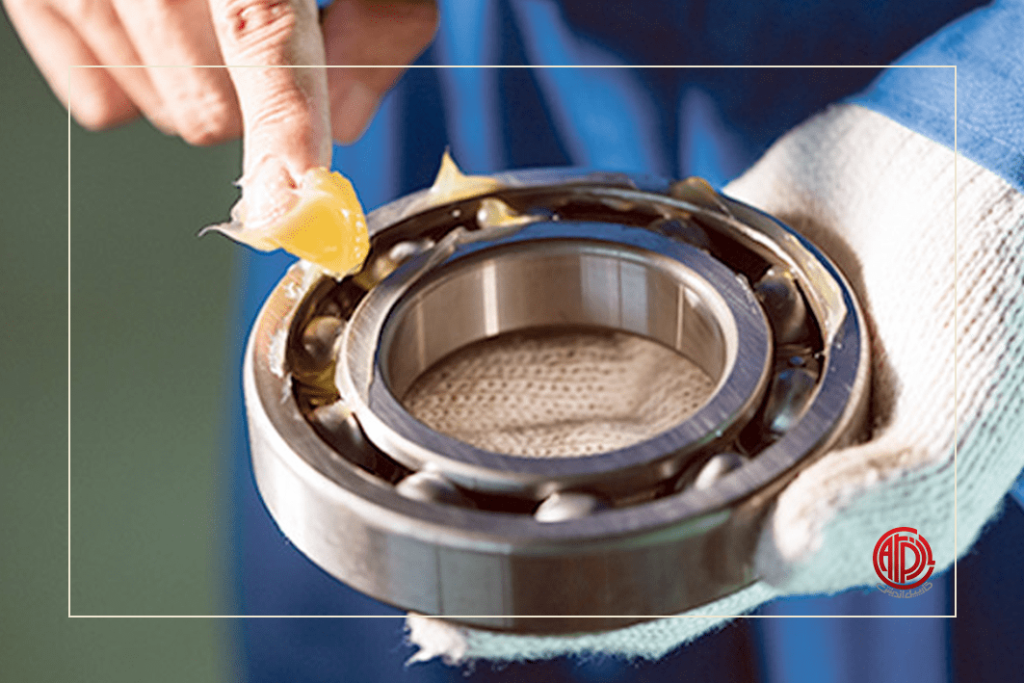
حمام روغن یا پاشش روغن
طریقه روغن کاری بلبرینگ به روش حمام روغن معمولا برای بلبرینگ های سایز بزرگ به کار می رود. محفظه بیرینگ تقریبا با روغن پر می گردند که اجزای مختلف در حال چرخیدن تحت پاشش روغن قرار می گیرند.
نظارت و نگهداری
نظارت مستمر بر وضعیت روان کننده و هم چنین عملکرد بلبرینگ ازضروریات است. در دستورات کاری خود قرار بدید که میزان روان کنندگی، کیفیت روان کننده و مقدار آلودگی را آنالیز کنید.برخی از نشانه ها نمایانگر وجود مشکل مقدار کم و ناکافی روغن هستند که باید به این علائم همواره توجه داشته باشید. از جمله این عوامل حرارت غیر معمول، لرزش و سر و صدا هستند. در این حالت با در نظر گیری دستورالعمل های تولید کننده، روغن را تعویض یا پر گردانید.
همواره بایستی این نکته را در نظر داشت که طریقه روغن کاری بلبرینگ با توجه به کاربرد آن و تجهیزات به کار رفته، متفاوت می باشد. پس برای به کارگیری روش اصولی و بهینه و افزایش طول عمر بیرینگ، بهترین راهکار خواندن دستورالعمل های تولید کننده، می باشد.
گریس کاری مجدد بیرینگ
از آنجایی که گریس ها دارای طول عمر معینی هستند، به هنگام استهلاک می بایست تعویض گردند. در صورتی که عمر گریسی که به کار بردید، کم تر از طول عمر بلبرینگ است، در فاصله های زمانی مشخص آن را تعویض نمایید. معیاری که این فاصله های زمانی را تعیین می کند، شامل مدل و سایز بیرینگ، بار موجود، سرعت چرخش، دما و نوع گریس می گردد.
- ZWZ Bearing
- استاندارد بلبرینگ چینی
- استعلام قیمت بلبرینگ
- انواع برند بلبرینگ
- انواع بلبرینگ zwz
- انواع بلبرینگ چینی
- انواع بلبرینگ و رولبرینگ
- انواع بلبرینگ*
- انواع سایزهای بلبرینگ
- انواع مختلف بلبرینگ
- بادوامترین بلبرینگ
- برترین برندهای بلبرینگ
- برترین بلبرینگ
- برترین سایت بلبرینگ
- برترین سایت بلبرینگ چینی
- برند zwz
- برند های بلبرینگ چینی
- بلبرینگ
- بلبرینگ skf
- بلبرینگ zwz
- بلبرینگ ارزان
- بلبرینگ ارزان قیمت
- بلبرینگ استوانه ای چیست ؟
- بلبرینگ اصل
- بلبرینگ اقتصادی
- بلبرینگ با کیفیت چینی
- بلبرینگ باکیفیت
- بلبرینگ به صرفه
- بلبرینگ تماس زاویه ای دوطرفه
- بلبرینگ چیست ؟
- بلبرینگ چینی
- بلبرینگ چینی اصل
- بلبرینگ چینی باکیفیت
- بلبرینگ چینی درجه یک
- بلبرینگ خود تنظیم شونده
- بلبرینگ درجه 1 چینی
- بلبرینگ زد دبلیو زد
- بلبرینگ ساخت چین
- بلبرینگ ساخت چین
- بلبرینگ شیار عمیق
- بلبرینگ شیار عمیق چیست ؟*
- بلبرینگ صنعتی
- بلبرینگ صنعتی zwz
- بلبرینگ کف گرد
- بلبرینگ کف گرد چیست ؟
- بلبرینگ مناسب قیمت
- بلبرینگ نسوز*
- به صرفه ترین خرید بلبرینگ
- بهترین برند برای خرید بلبرینگ چینی کدام است ؟
- بهترین برند بلبرینگ چینی
- بهترین بلبرینگ چینی
- بهترین راه برای اطمینان از بلبرینگ ؟
- بهترین قیمت بلبرینگ چینی
- بهترین گریس برای بلبرینگ
- پخش بلبرینگ چینی
- پخش کننده بلبرینگ در تهران
- پرداخت
- پمپ صنعتی
- تاریخچه بلبرینگ
- تامین کننده بلبرینگ
- تجهیزات صنعتی
- تست بلبرینگ
- تست بلبرینگ چینی
- تضمین اصالت بلبرینگ
- تماس با ما :
- توربین بادی
- جنس بلبرینگ
- حساب کاربری
- حفاری معادن ، سیمان ، فولاد
- حمل و نقل ریلی
- خرید بلبرینگ
- خرید بلبرینگ zwz
- خرید بلبرینگ به صرفه
- خرید بلبرینگ چینی
- خرید بلبرینگ در تهران
- خرید عمده بلبرینگ چینی
- درباره ما
- راحت ترین راه برای نصب بلبرینگ
- روانکاری بلبرینگ
- روش نصب بلبرینگ
- رولبرینگ zwz
- رولبرینگ استوانه ای**
- رولبرینگ بشکه ای
- رولبرینگ بشکه ای*
- رولبرینگ تماس زاویه ای**
- رولبرینگ مخروطی
- ساخت بلبرینگ
- سایت بلبرینگ
- سایز بلبرینگ
- سایز های بلبرینگ چینی
- سبد خرید
- شرکت کارپیل اندیش نماینده رسمی دو برند ZWZ , TMB
- صنعت نفت و گاز و پتروشیمی
- عرضه کننده بلبرینگ
- عوامل مهم در انتخاب بلبرینگ
- عوامل موئثر بر قیمت بلبرینگ چیست ؟
- فروش اینترنتی بلبرینگ
- فروش بلبرینگ
- فروش بلبرینگ به صرفه
- فروش بلبرینگ چینی
- فروش بلبرینگ صنعتی
- فروشگاه بلبرینگ
- قیمت zwz
- قیمت بلبرینگ zwz
- قیمت بلبرینگ استوانه ای
- قیمت بلبرینگ استوانه ای zwz
- قیمت بلبرینگ تماس زاویه ای
- قیمت بلبرینگ چین چطور محاسبه میشه ؟
- قیمت بلبرینگ چینی
- قیمت بلبرینگ چینی zwz
- قیمت بلبرینگ خود تنظیم شونده
- قیمت بلبرینگ شیارعمیق
- قیمت بلبرینگ صنعتی
- قیمت بلبرینگ کف گرد
- قیمت رولبرینگ بشکه ای
- قیمت رولبرینگ مخروطی
- کار با بلبرینگ
- کاربرد بلبرینگ در صنعت
- کاسه نمد
- کیفیت بلبرینگ چینی
- لیست قیمت بلبرینگ چینی
- لیست محصولات بلبرینگ های کف گرد
- ماشین آلات سبک،سنگین
- مشخصات نمایندگی رسمی بلبرینگ
- معروفترین بلبرینگ چینی
- مقایسه بلبرینگ سرامیکی و فولادی
- مقرون به صرفه ترین بلبرینگ
- نکات مهم در خرید بلبرینگ ZWZ چیست ؟
- نمایندگی بلبرینگ
- نمایندگی بلبرینگ چینی
- نمایندگی رسمی zwz
- نمایندگی رسمی بلبرینگ
- نمایندگی معتبر بلبرینگ
- نماینده رسمی بلبرینگ TMB
- نماینده رسمی بلبرینگ های ZWZ
- نماینده فروش بلبرینگ
- همه چیز درباره خریداری بهترین بلبرینگ ؟
- وارد کننده بلبرینگ
- واردات بلبرینگ چینی
- واردکننده بلبرینگ صنعتی در ایران
بهترین گریس ها جهت روانکاری بلبرینگ چه نوع گریس هایی می باشد ؟
انتخاب بهترین گریس برای روانکاری بلبرینگها به چند عامل بستگی دارد، از جمله نوع کاربرد، شرایط محیطی (دمای کارکرد، رطوبت، فشار و غیره) و نوع بلبرینگ. در اینجا انواع گریسهایی که معمولاً برای روانکاری بلبرینگها توصیه میشوند و بهترین گزینهها را در شرایط مختلف معرفی کردهام:
گریسهای پایه لیتیم (Lithium-based Grease):
- ویژگیها: یکی از رایجترین و پرکاربردترین انواع گریسها هستند. گریسهای پایه لیتیم به دلیل قابلیت تحمل دمای بالا، چسبندگی خوب، و مقاومت در برابر اکسیداسیون محبوب هستند.
- مزایا:
- عملکرد خوب در دماهای 20 تا 130 درجه سانتیگراد.
- مقاوم در برابر آب و رطوبت.
- مقاومت خوب در برابر فشارهای متوسط.
- استفاده مناسب: برای بلبرینگهای معمولی و در شرایط استاندارد (در صنایع خودروسازی، صنایع عمومی و حتی در بلبرینگهای خانگی و صنعتی).
گریسهای پایه کلسیم (Calcium-based Grease):
- ویژگیها: این نوع گریسها دارای خواص ضدآب بالایی هستند و در محیطهای مرطوب و یا در تماس با آب به خوبی عمل میکنند.
- مزایا:
- مقاوم در برابر آب.
- مناسب برای شرایط مرطوب.
- استفاده مناسب: برای بلبرینگهایی که در محیطهای مرطوب یا در تماس با آب قرار دارند (مثلاً در صنایع دریایی و کشاورزی).
گریسهای پایه پلیآلکیلامید (Polyalkylene Glycol-based Grease):
- ویژگیها: این نوع گریسها برای شرایط دمایی و فشار بالا مناسب هستند و در برابر مواد شیمیایی مقاومت خوبی دارند.
- مزایا:
- عملکرد عالی در دماهای بالا و فشارهای شدید.
- مقاوم در برابر مواد شیمیایی.
- استفاده مناسب: در صنایع شیمیایی و نفت و گاز و همچنین در بلبرینگهایی که در شرایط دمایی بالا و فشار زیاد کار میکنند.
گریسهای سیلیکونی (Silicone-based Grease):
- ویژگیها: این گریسها در دماهای بسیار بالا (تا 250 درجه سانتیگراد) عملکرد خوبی دارند و به دلیل پایه سیلیکونی، ضدآب و مقاوم در برابر اکسیداسیون هستند.
- مزایا:
- مقاوم در برابر دماهای بسیار بالا.
- مناسب برای کاربردهای خاص مانند بلبرینگهای در محیطهای داغ.
- استفاده مناسب: برای بلبرینگهایی که در محیطهای داغ، مانند صنایع کورهسازی یا تجهیزات گرمایی و برودتی، مورد استفاده قرار میگیرند.
گریسهای لیتیوم-کلسیم (Lithium-Calcium Grease):
- ویژگیها: ترکیب دو نوع پایه لیتیم و کلسیم این گریسها باعث میشود که هم از مزایای گریسهای لیتیم و هم از مزایای گریسهای کلسیم بهرهمند شوند.
- مزایا:
- مقاوم در برابر فشار.
- عملکرد خوب در دماهای بالا و شرایط مرطوب.
- استفاده مناسب: برای بلبرینگهایی که هم در شرایط فشار بالا و هم در محیطهای مرطوب کار میکنند.
گریسهای PTFE (Teflon-based Grease):
- ویژگیها: گریسهای با افزودن PTFE (تفلون) به مواد پایه، خاصیت لغزندگی و مقاومت در برابر اصطکاک و سایش را افزایش میدهند.
- مزایا:
- کاهش اصطکاک و سایش.
- عملکرد عالی در دماهای بسیار بالا و شرایط خشک.
- استفاده مناسب: برای بلبرینگهایی که در شرایط خشک و دمای بالا یا فشار زیاد کار میکنند.
گریسهای آلومینیومی (Aluminum Complex Grease):
- ویژگیها: این نوع گریسها مقاومت بالایی در برابر دماهای بالا و آب دارند و از نظر ساختار بسیار پایدار هستند.
- مزایا:
- عملکرد عالی در دماهای بالا (تا حدود 180 درجه سانتیگراد).
- مقاومت عالی در برابر رطوبت.
- استفاده مناسب: در بلبرینگهای کاربردی در شرایط دمایی بالا و محیطهای مرطوب (مثلاً در صنایع خودروسازی و تجهیزات صنعتی سنگین).
نکات مهم در انتخاب گریس برای بلبرینگ:
- دمای کارکرد: مهمترین عامل انتخاب نوع گریس، دمای کارکرد بلبرینگ است. هر گریس در دمای خاصی بهترین عملکرد را دارد.
- رطوبت و آب: اگر بلبرینگ در معرض آب یا رطوبت است، باید از گریسهایی استفاده کنید که مقاوم در برابر آب باشند.
- نوع بار و فشار: برای بلبرینگهایی که تحت فشار زیاد قرار دارند، گریسهایی با مقاومت بالا در برابر فشار مناسبتر خواهند بود.
- سازگاری با مواد شیمیایی: اگر بلبرینگ در معرض مواد شیمیایی یا آلایندهها قرار دارد، باید گریسهایی انتخاب کنید که در برابر مواد شیمیایی مقاوم باشند.
توصیههای عمومی:
- پیشگیری از روغنکاری بیش از حد: همیشه به میزان گریس مورد نیاز توجه کنید. گریس زیاد میتواند منجر به افزایش دمای بلبرینگ و کاهش عمر آن شود.
- برندهای معتبر: برندهایی مانند Shell, Mobil, SKF, Castrol, Total و Liqui Moly گریسهایی با کیفیت بالا تولید میکنند که معمولاً در صنایع مختلف استفاده میشوند.
با توجه به شرایط خاص کاربرد بلبرینگ، انتخاب گریس مناسب میتواند عمر مفید بلبرینگ را افزایش دهد و عملکرد بهینه را تضمین کند.
آدرس فروشگاه :
آدرس: سعدی جنوبی، خیابان اکباتان، کوچه ناظم الاطبا شمالی، پاساژ مبصر، طبقه همکف، پلاک 15
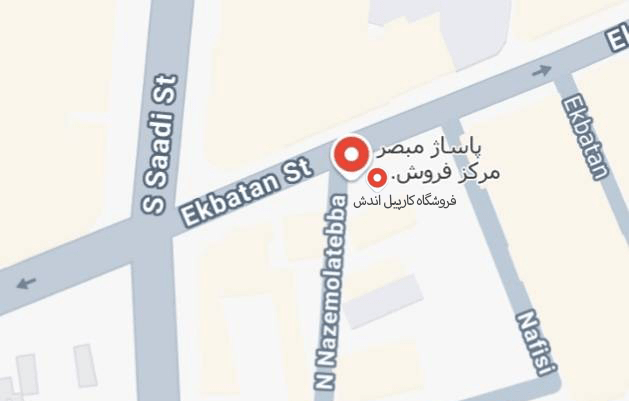
آدرس دفتر :
تهران ، شهرک غرب ، بلوار فرحزادی ، بلوار نورانی ، پلاک 36
تلفن فروشگاه :
021-33996881
021-33996882
تلفن دفتر :
021-88562390
021-88562210
ایمیل :
info @carpil-co.com
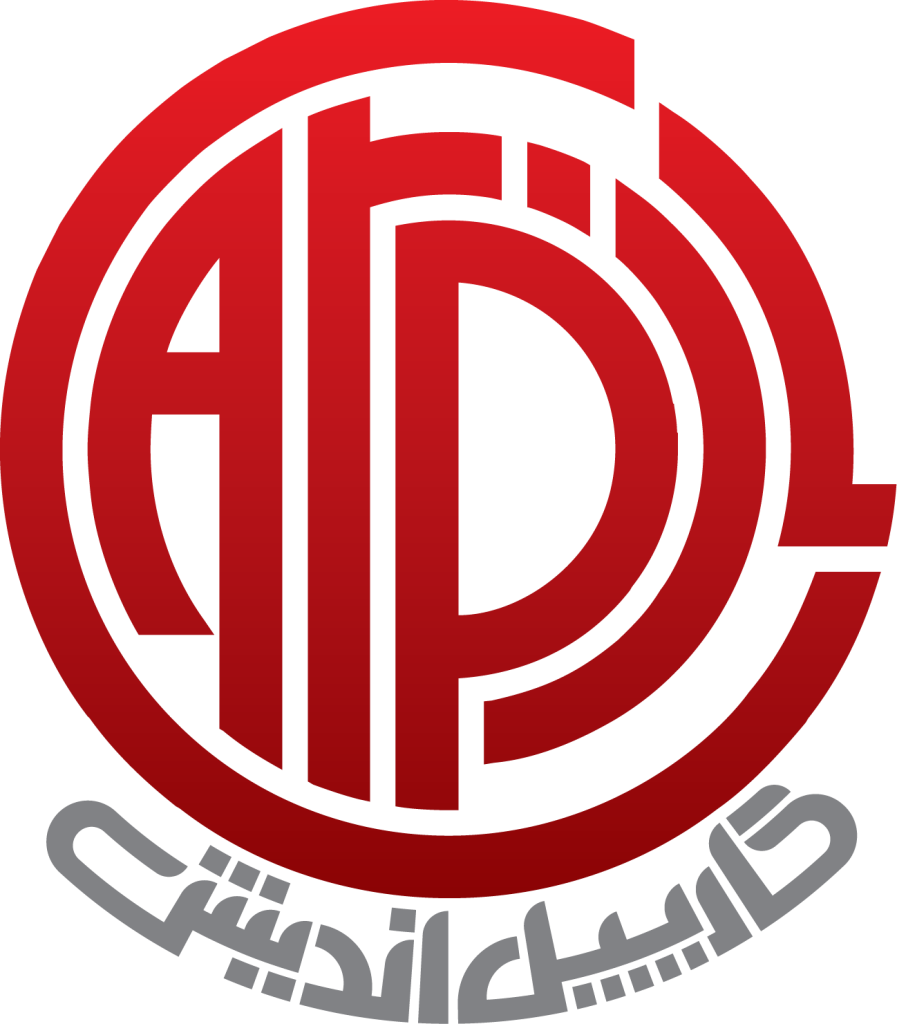
شبکه های اجتماعی ما :
واتساپ :
09199068526
تلگرام :
09199068526
اینستاگرام :
carpil andish
09
دیدگاهتان را بنویسید